Coventor
Coventor® , a Lam Research company, is a market leader in automated solutions for developing semiconductor process technology, as well as micro-electromechanical systems (MEMS).
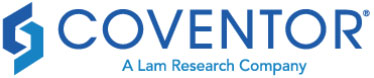
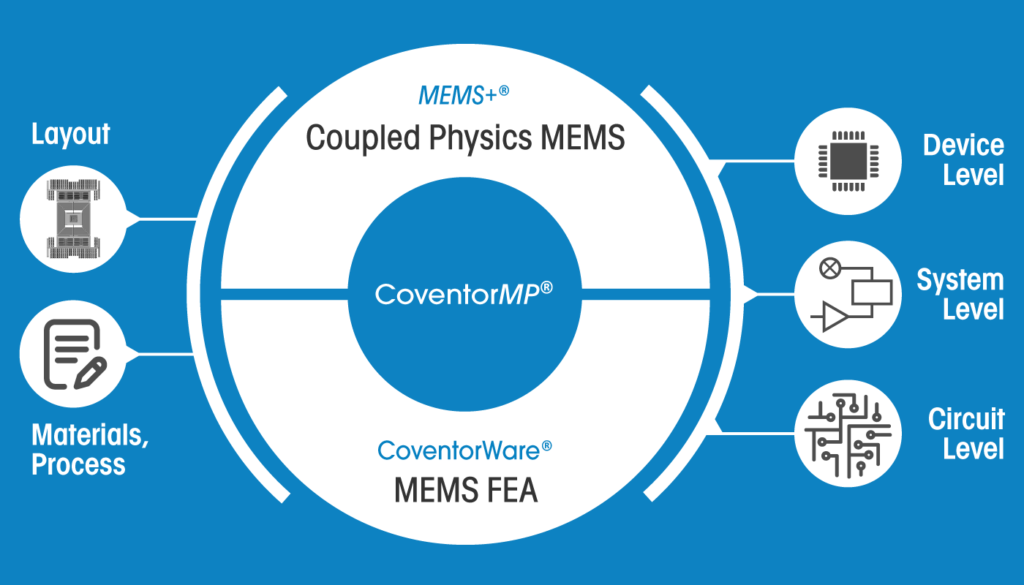
CoventorMP
Coventor offers integrated products for MEMS design: CoventorMP®, MEMS+® and CoventorWare®.
CoventorMP Software Features
CoventorMP combines the complementary strengths of Coventor’s industry-leading software tools for MEMS design, CoventorWare® and MEMS+®, into a single powerful environment for MEMS design automation. The new platform provides a cohesive environment where designs can be entered once and used to create conventional finite element models (CoventorWare) and compact finite element models (MEMS+).
The CoventorMP platform provides a unified environment for MEMS design, starting from fully parametric design entry to the production of functional models that can be simulated at all levels of abstraction.
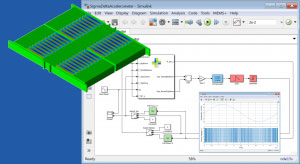
MEMS+
Rapid design exploration and optimization. Models are assembled from a library of parametric, high-order finite elements and can simulate up to 100X faster than conventional FEA, enabling
- Modal analysis
- Quasi-static coupled electro-mechanics (pull-in, lift-off, electrostatic spring softening)
- Harmonic analysis
- Sensitivity studies of design and fabrication variables
- Transient simulations of electro-mechanical behavior fully coupled with gas damping effects
- Closed-loop system simulation in Simulink and Cadence
- Noise analysis in Cadence Spectre and APS simulators
- Inclusion of package/substrate deformation effects on sensor performance
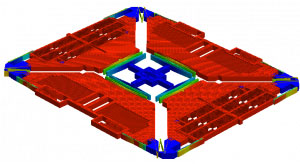
CoventorWare
Detailed device analysis with a suite of FEM/BEM solvers. The 2D-to-3D model builder, automatic meshing and field solvers are optimized for MEMS structures and multi-physics, addressing most types of MEMS:
- Modal analysis
- Quasi-static coupled electro-mechanics (pull-in, lift-off, electrostatic spring softening)
- Harmonic analysis
- Fast-frequency-sweep algorithm for piezoelectric BAW resonators
- Gas damping for any 3D geometry
- Energy dissipation from thermo-elastic damping and anchor losses
- Sensitivity analysis of piezo-resistive sensors
- Detailed stress analysis
MEMS+
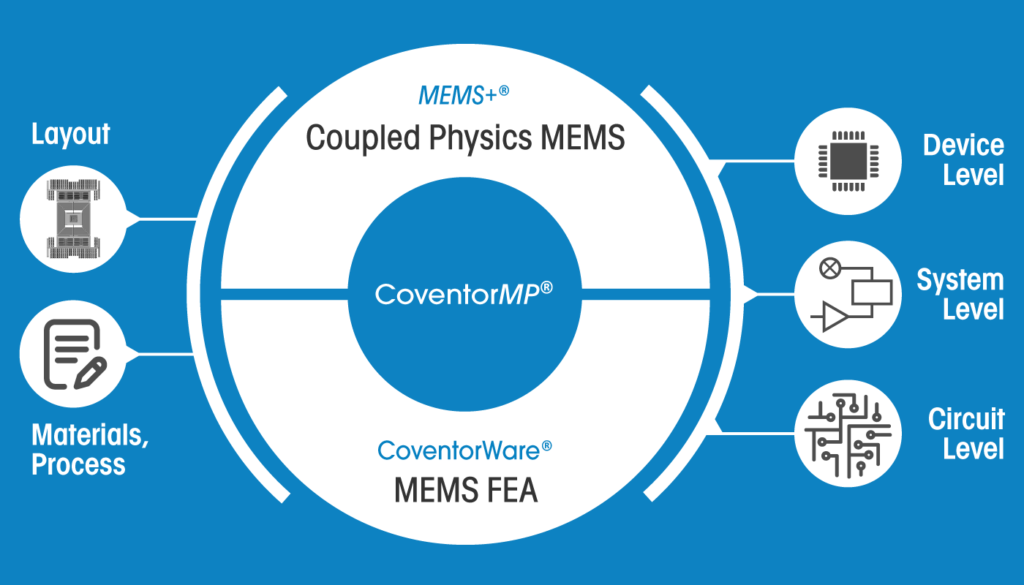
Key Benefits of MEMS+
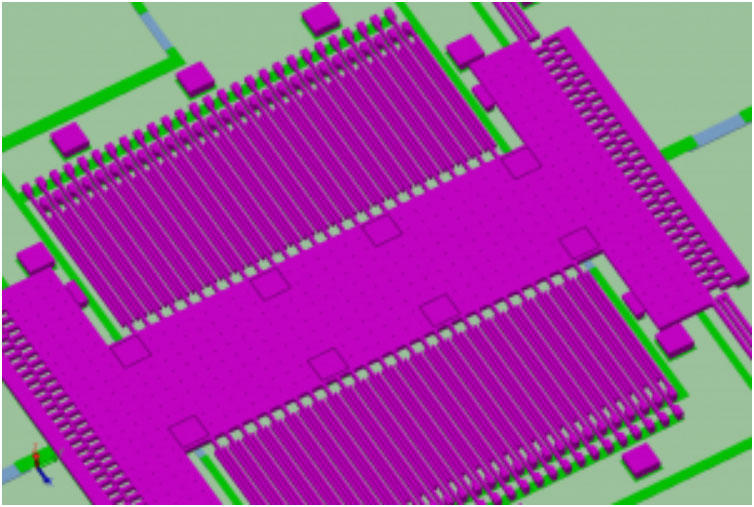