Simcenter
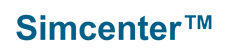
Why Simcenter?
Model the complexity
Explore the possibilities
Go faster
Stay integrated
Better together
Simcenter for Computational Fluid Dynamics
Engineering Innovation with multiphysics computational fluid dynamics (CFD) simulation software.
Discover how engineers, from designers to analysts, can:
- Model the complexity with multiphysics CFD and accurate CAD handling
- Go faster with automated end-to-end and application-specific CFD workflows
- Make critical design decisions earlier with CAD-embedded CFD
- Explore the possibilities with fully-integrated design exploration
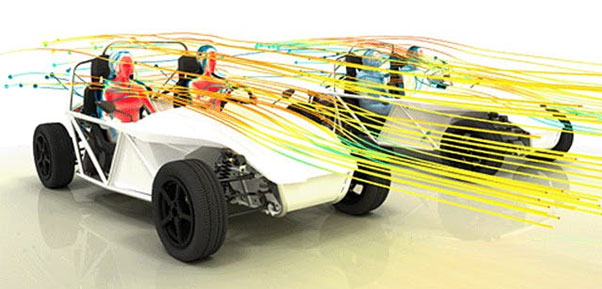
Simcenter StarCCM+
Why Simcenter StarCCM+?
Boost your productivity with a fully integrated user interface
Cope with the most complex applications
Cover physics way beyond fluid flow and heat transfer. This fully integrated solver platform allows you to run even the most complex multiphysics CFD simulations.
Cut CFD preparation times
Leverage powerful end-to-end, code-free workflow automation and fully embedded design exploration
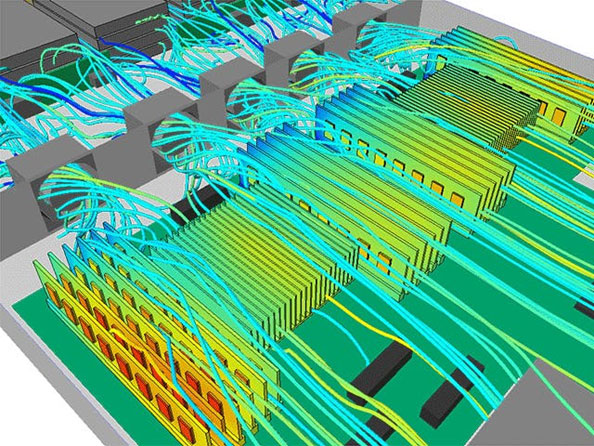
Simcenter FloTherm
Why Simcenter Flotherm?
Accelerate electronics thermal design workflow
Simcenter Flotherm integrates with the electronics development workflow as a tool for thermal engineers to perform simulation and provide timely accurate results and feedback to other engineering functions. It supports thermal management, simulation-based decision making from early-stage architecture to final thermal design verification. This aids shortened development, and also helps to eliminate risks of costly reliability-related warranty costs or any late-stage re-spins.
Example capabilities that help engineers shorten the thermal analysis process include: innovative SmartPart technology, extensive libraries, EDA and MCAD data handling, a tailored and stable solver technology, state-of-the art compact thermal modeling techniques, automatic model calibration through to parametric analysis and optimization functionality.
Leverage accurate, fast thermal analysis
Reduce model creation time with intelligent SmartParts
Incorporate EDA and mechanical design data complexity during development
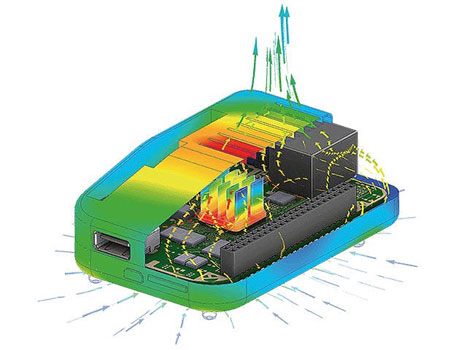
Simcenter FloTherm XT
Why Simcenter Flotherm XT?
Compress the electronics thermal design process
Incorporate EDA data quickly
Reduce model creation time with intelligent SmartParts
Handle CAD geometry complexity with a CAD-centric interface
Perform parametric studies and thermal management optimization
Make the most of an integrated environment for defining, solving and analyzing results using parametric variations of geometry, attributes plus solution parameters to optimize your thermal design. You can use Design of Experiments to set up a number of studies, varying parameters and ensuring the best coverage of the design field.
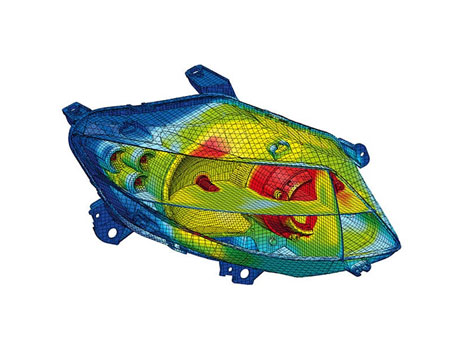
Simcenter FLOEFD
Why Simcenter FLOEFD?
Simcenter FLOEFD is a fully CAD-embedded CFD software with Multiphysics capabilities for designers to analysts. It helps shorten development by up to 65-75% compared to typical CFD approaches by frontloading fluid flow simulation and thermal analysis using native CAD geometry.
Frontload CFD simulation to shorten development
Simcenter FLOEFD enables design engineers to perform simulation earlier in the design process when it is more cost-effective to identify and fix problems or explore improvements. Integrated in CAD, it has shown improved productivity by a factor of x2 to x40.
Leverage an intuitive CFD interface for designers
Perform CFD directly on native CAD geometry and eliminate CFD overheads
Eliminate delays in geometry translation between tools and overcome complexity in preparing CAD geometry for CFD analysis. Simcenter FLOEFD uses native geometry directly: so as you explore performance or evaluate changes to a model, the CAD model is being changed concurrently.
It has key strengths in robust automatic meshing and unique SmartCell technology that enables handling of CAD geometry of any quality. These strengths help to handle small narrow gaps in assemblies and surface inconsistencies, which often cause long delays for healing in traditional CFD tools. This is complemented by intelligent automation for pre-processing, such as automatic sealing of CAD geometry and leak identification.
Use simulation driven design – explore, compare and optimize
Leverage parametric studies and design exploration functionality to evaluate more design options within the time available. Evaluate ‘what if’ scenarios to ensure product performance and reliability in different conditions.
Using the software, engineers can easily compare designs side-by-side with CFD result visualizations, plots, and tabulated results and generate reports in just a few clicks. When the designs are optimized using simulation, you can directly communicate the CAD model to other engineering functions.
SIMCENTER MECHANICAL SIMULATION
Model the complexity, reduce prototypes
Use mechanical simulation tools to:
- Predict mechanical performance across multiple physics domains reducing reliance on physical prototypes.
- Speed the simulation process to rapidly evaluate product performance and iterate on designs.
- Simulate accurately and reliably with industry-leading solvers for computational performance and scalability.
- Streamline complex, Multiphysics analyses through integrated simulation tools.
Simcenter 3D software
Why Simcenter 3D?
Go faster – through a common engineering desktop
Model the complexity – by simulating many physics phenomena
Explore the possibilities – through simulation automation
Stay integrated – through seamless data management
Enjoy flexible licensing
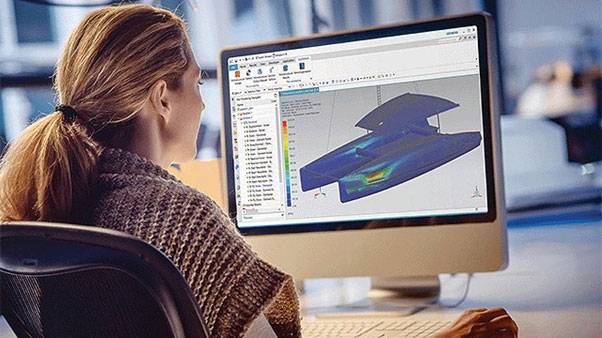
Simcenter 3D modelling software capabilities
Integrated, multidiscipline pre-/post-processing
At the heart of Simcenter 3D is a centralized working environment for pre-/post-processing of all Simcenter 3D solutions for structural, dynamics, composites, durability, acoustics, thermal, flow, motion, optimization and electromagnetics. This integrated environment helps you to achieve faster CAE processes and streamline multidiscipline simulations that integrate any of the Simcenter 3D solutions together, like thermal-mechanical, vibro-acoustic or other more complex analyses. Simcenter 3D’s pre/post helps you to:
- Quickly and intuitively edit, defeature and abstract geometry
- Build any kind of mesh with comprehensive meshing tools
- Efficiently create and manage finite element (FE) assemblies
- Create, run and evaluate simulation models for multiple common third-party CAE solvers
- Efficiently launch and monitor simulations remotely
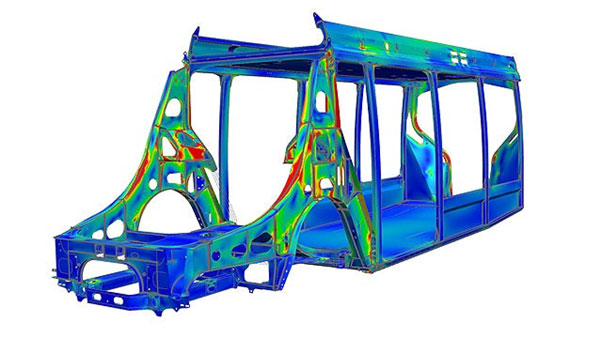
Structural analysis
Simulate structures to understand how they perform for stress, deformation and more. Structural analysis solutions within Simcenter 3D are powered by the well-known Simcenter Nastran solver and can help you accurately simulate the following types of solutions:
- Linear analysis
- Multistep nonlinear analysis
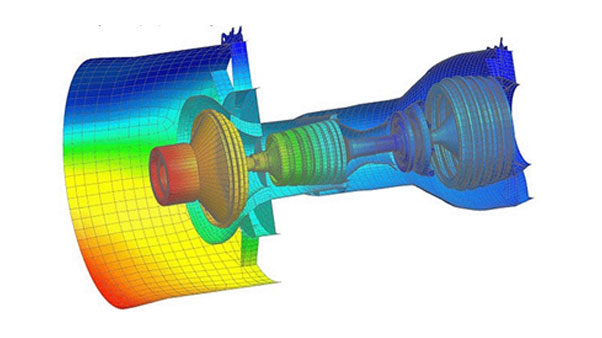
Structural dynamics
Understand, analyze and improve structural dynamics response. Simcenter 3D structural dynamics solutions help you to efficiently understand and avoid excessive vibrations and stresses. Dedicated capabilities available within the structural dynamics solution include:
- Structural dynamics
- Noise, vibration and harshness (NVH)
- Rotor dynamics
- Response dynamics
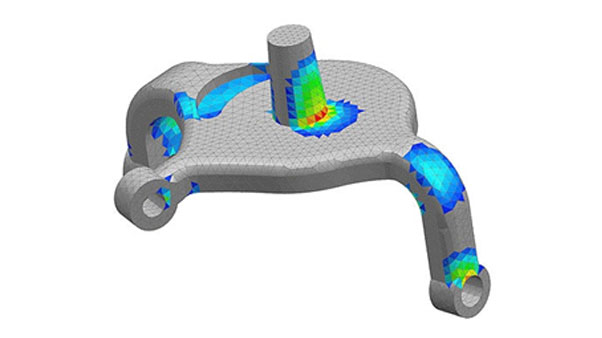
Durability and fatigue analysis
Perform in-depth fatigue and lifing analysis through an integrated suite of tools to support fatigue design in all stages of development. This includes easy-to-use wizards for strength and fatigue in the design phase; fatigue information on the current simulated part; detailed analysis of complex load scenarios, including weldments and connections; and new materials and manufacturing processes. Specific capabilities for durability include:
- Fatigue strength analysis
- Weld fatigue
- Composite fatigue
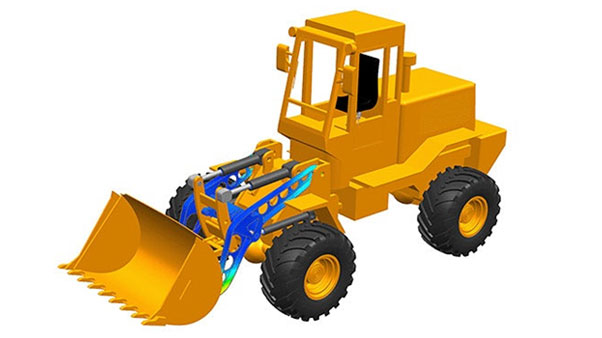
Motion simulation
Simulate multibody dynamics to engineer performance for moving mechanisms. Simcenter 3D includes a complete and robust set of capabilities to support all aspects of advanced dynamic, static and kinematics motion simulation. The early use of motion simulation is key to evaluating mechanism performance to increase design confidence and reduce risks. Specific capabilities include:
- Rigid body and flexible body dynamics
- Control system integration
- Drivetrain, transmission and gears
- Interference checking
- Hardware-in-the-loop (HIL)
- Time waveform replication
- Driving dynamics
- Tire model integration
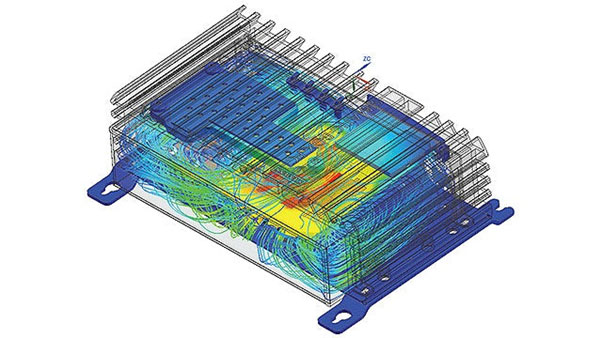
Thermal analysis
Simcenter 3D is a complete solution for modeling nonlinear and transient heat transfer phenomena. Dedicated thermal modeling capabilities help you rapidly create thermal connections, select the right physical model and define the right loads and boundary conditions. Simcenter 3D thermal analysis solutions include these specific capabilities:
- Conduction heat transfer
- Convection heat transfer
- Radiation heat transfer
- Conjugate heat transfer
- Space-systems thermal
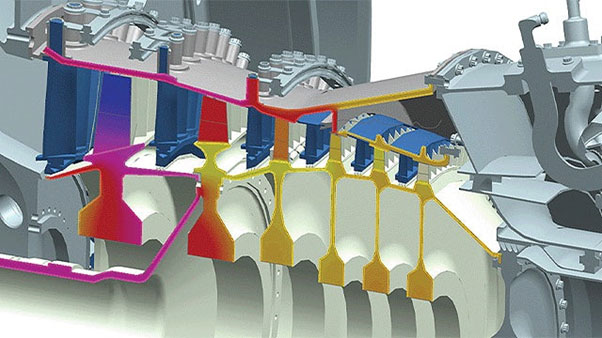
Multiphysics
Integrate domain solutions to solve real-world problems. Simcenter 3D streamlines multiphysics simulation through a common engineering desktop that is used for pre- and post-processing of multiple disciplines. Through this integrated platform, you can more easily perform multiphysics simulations such as thermal-fluid, thermo-mechanical, fluid-structure interaction, vibroacoustics, aero-vibro-acoustics, electromagnetic-thermal and electromagnetic-vibro-acoustic. Simcenter 3D also supports both weak and strong coupling depending on the physics types involved. Simcenter 3D performs multiphysics simulations using these different methods:
- One-way data exchange
- Two-way data exchange
- Integrated coupled solutions
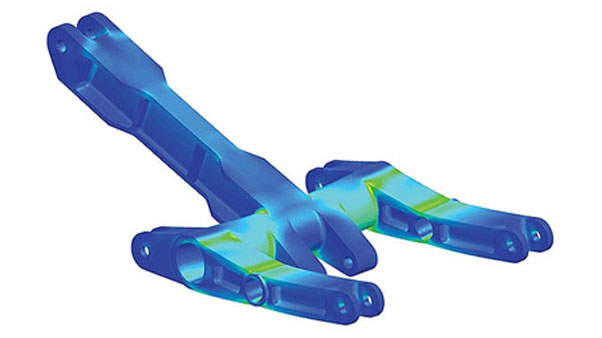
Design space exploration and optimization
Improve and optimize your product designs. Simcenter 3D software optimization solutions relieve the burden of improving product designs by automating the iterative process. This enables you to compare your design’s performance against specifications. It also enables you to start at topology optimization and extend to design space exploration with more classical parametric optimization capabilities. Specific design space exploration and optimization capabilities include:
- Integrated design-space exploration
- Topology optimization
- FE parameter optimization
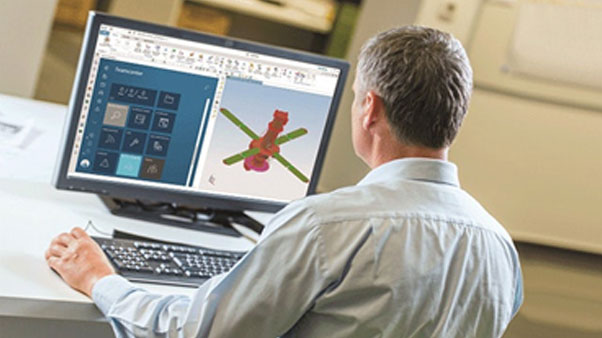
Seamless data management
Trace all of your team’s simulation work and data in a product development context. You can use Simcenter 3D in a seamlessly managed environment integrated with Teamcenter software. When Simcenter 3D is used with Teamcenter integration, you can create, store and access your product simulation data in a Teamcenter database. It combines the power of Simcenter 3D in multiphysics modeling with the power of Teamcenter in storing and retrieving data in a controlled fashion. Capabilities include:
- Integration with Teamcenter simulation
- Rules-based assembly management
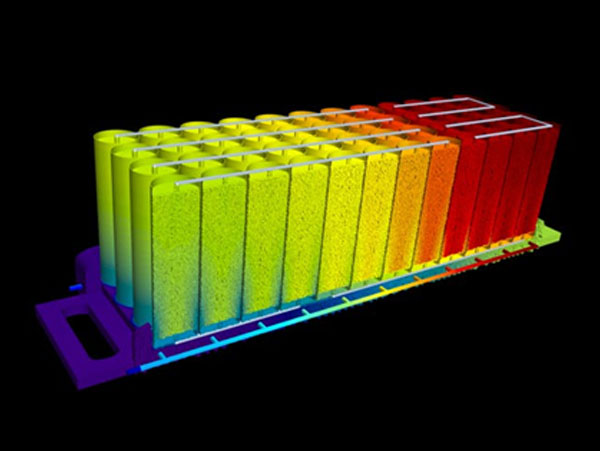
Simcenter BDS
Why Simcenter Battery Design Studio?
Simcenter Battery Design Studio supports engineers in digitally validating Li-ion cell designs thanks to detailed geometrical cell specifications and cell performance simulations. Extensive components of a battery cell are available, as well as a material database to support your model development.